‘Smart propellers’ for greater drone safety
Fraunhofer Institutes develop self-monitoring propellers for improved drone performance
Intelligent technology for maximum safety
Researchers at the Fraunhofer Institutes IMS, IOSB and IVI have developed a pioneering technology that sets new standards for the safety and reliability of drone systems. By integrating advanced sensors directly into the propeller blades, they have created a ‘smart propeller’ that can monitor its own condition in real time. The elastic deformation of the propeller geometry, vibrations and shocks as well as the temperature during operation are recorded.
This innovation has the potential to fundamentally change the drone industry. ‘By integrating sensors into the propeller blades, we can detect potential damage at an early stage and thus minimise the risk of crashes,’ explains Dr Alexander Utz, head of the System on Chip group at Fraunhofer IMS.
New standards for condition monitoring
A microcontroller processes the sensor signals and transmits the data wirelessly to the drone's on-board control system. The collected information can be analysed in real time to monitor the condition of the propeller and detect potential deviations at an early stage.
This prevents costly failures and minimises risks. Continuous monitoring also makes it possible to plan and carry out maintenance work in a more targeted manner. Ultimately, the real-time data can be used to optimise the flight parameters.
The intelligent propellers can be integrated into drone systems in a variety of ways. The use of drones offers enormous potential for various industries, including
· Agriculture: Precise monitoring of fields and accurate application of pesticides
· Search and rescue: Effective search for missing persons in rough terrain
· Delivery services: Safe and reliable delivery of parcels in all weather conditions
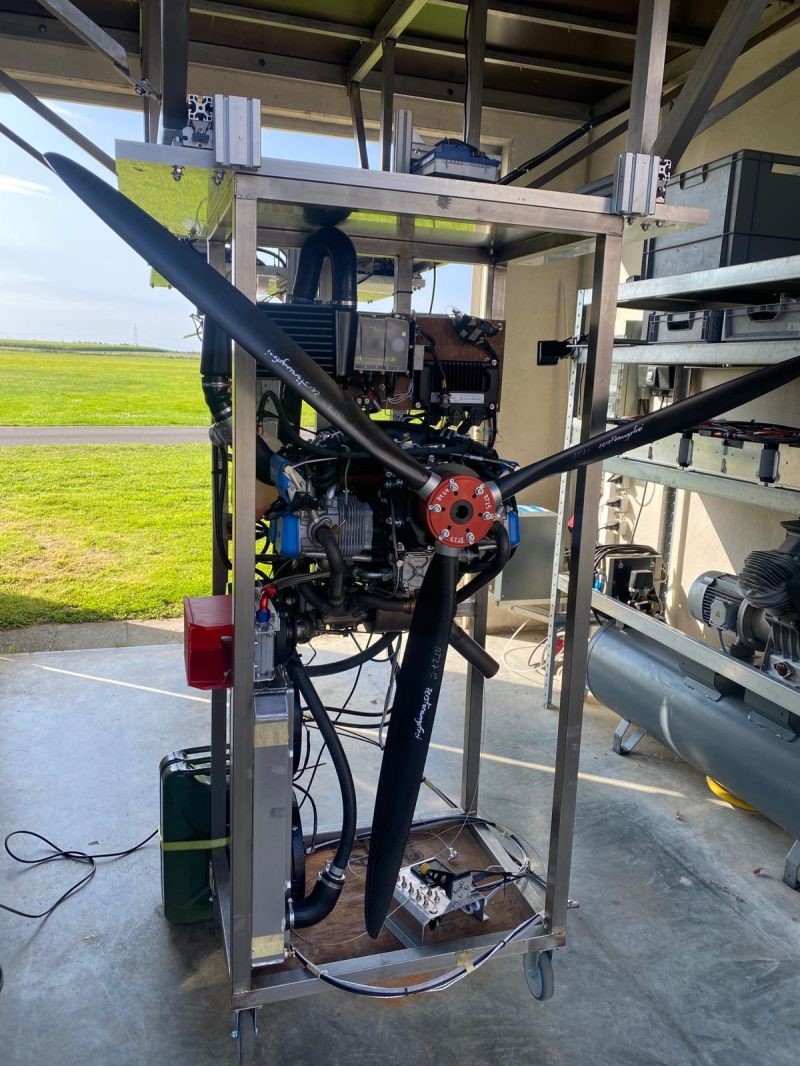
Innovative production technologies for intelligent propellers
The propeller blades are manufactured using High Pressure Resin Transfer Moulding (HP-RTM), a special process that is suitable for large-scale production. In this process, several layers of particularly light and stable carbon fibres are laid along a foam core. In the next step, this so-called preform is impregnated with a special resin and cured at 120 °C.
During this preforming process, the tiny sensors are carefully placed between the individual layers. The result is an extremely stable and lightweight propeller in which the sensors are firmly bonded to the material and can precisely measure the smallest changes.
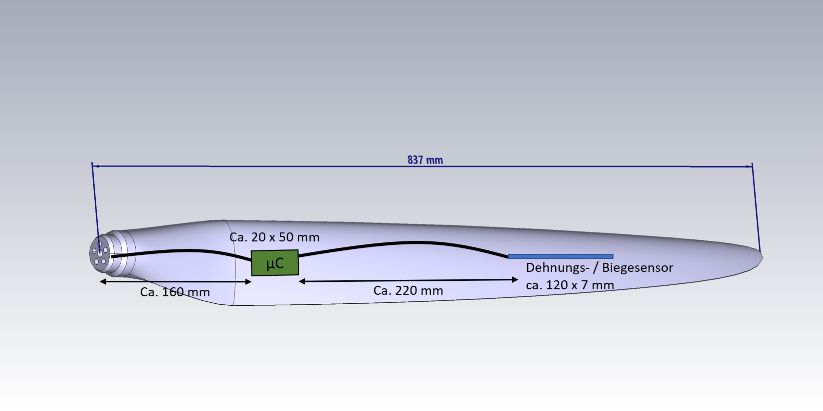
Seamless integration into the on-board electronics
The sensor data is transmitted to a communication module in the ALBACOPTER®. This module acts as a central collection point for all information available to the drone. The data is then sent to the ground station via a 5G mobile phone connection.
There it can be analysed live by the pilots or technical staff. At the same time, the data is also stored in the drone itself so that it can be precisely analysed again later. As the module in the ALBACOPTER® is already designed for the wireless transmission of data, the sensor data from the propeller can be seamlessly integrated into the existing system.
The developments therefore provide a solid basis for future research projects and commercialisation in collaboration with industry.
About ALBACOPTER®
ALBACOPTER® is a Fraunhofer lead project with a project budget of eight million euros. It is funded by the Fraunhofer-Gesellschaft. The ‘smart propeller’ is being developed by the IMS, IOSB and IVI institutes, while the lead project involves a total of six Fraunhofer Institutes. The project is being coordinated by the Fraunhofer Institute for Transportation and Infrastructure Systems IVI.
Project website: https://www.albacopter.fraunhofer.de/en.html
About Fraunhofer flagship projects
Fraunhofer is tackling the current challenges facing industry head on. Its lighthouse projects put the focus on strategic objectives with a view to developing practical solutions from which economies such as Germany’s can benefit. The topics these projects address are geared towards economic requirements. By pooling their expertise and involving industrial partners at an early stage, the Fraunhofer Institutes involved in the projects aim to turn original scientific ideas into marketable products as quickly as possible.
Fraunhofer IMS
Smart Sensor Systems for a safe, secure, and sustainable future: In numerous state-of-the-art research laboratories, Fraunhofer IMS works with more than 200 talented scientific employees and students on innovative microelectronic solutions. As a trusted research and development partner for industry, the institutes’ goal is to develop customized sensor systems for your specific needs in the areas of biomedical sensors, optical systems, open source semiconductors, embedded AI, technology services, and even quantum technology. The teams in the four business units – Health, Industry, Mobility, and Space and Security – are committed to implementing outstanding and versatile microelectronics that can be utilized across all your projects. For example, these solutions feature high integration capability, enormous energy efficiency and reliable functionality even under harsh conditions.