Research and Development | Shortnews | Reading Time: 2 Min.
Increasing food quality and reducing recall costs through smart sound sensor technology: successful conclusion of BMWK project ISEP
Prevention of food contamination through AI-based monitoring methods
Defective equipment and contamination of food are the second-most common cause of food warnings in Germany. In the ISEP[1] project, Fraunhofer IMS has developed a solution that quickly and reliably detects such defects for each individually filled bag. This ensures a higher quality of the goods. Associated with this, food waste as well as high claims for damages and recall costs can be avoided in the future.
More safety and quality in our food and lower damage costs
In the ISEP project, research was conducted on the development of a flexible sound sensor for autonomous monitoring of processes in food production. The project aimed to develop a more reliable method of measuring a difficult-to-detect machine condition than previous models in order to prevent contamination in food products.
Reference processes for the project include filling lines, conveyors, and dosing systems from the food industry. As an example, a form fill and seal machine for filling foodstuffs such as powdered milk, coffee beans, or couscous was considered. Through targeted optimization, the condition detection of the dosing screw was continuously improved. Even under difficult conditions, such as the comparatively large and noisy coffee beans in the filling process, reliable monitoring of the status is possible.
The sound analysis proceeds in the following steps: first, feature extraction is used to reduce the collected data to the information relevant for evaluation. Then, an artificial neural network evaluates the remaining information. Both steps are integrated into an evaluation unit with a microcontroller connected to the sound sensor. The sensor is configured automatically on the basis of the training data already collected.
Perspective: Cost-sensitive training through automated fault detection
The ISEP project was successfully completed on May 31, 2023. In perspective, the next step will be to conduct research into automated defect detection for the various filling processes. Until now, extensive training data from functioning and defective equipment has been required to ensure the sensitivity of the sensor. This requires the targeted generation of different defects, which causes additional costs and jeopardizes the reuse of the machines. In contrast, automated defect detection would allow efficient sensor training only working data.
[1] ISEP is an acronym for: Intelligent Sound Sensor for Real-Time Monitoring of Production Processes. This project is funded by the German Federal Ministry of Economics and Climate Protection (BMWK) based on a resolution of the German Bundestag - under the funding code 16KN085620. The project was carried out in cooperation with ds automation GmbH.
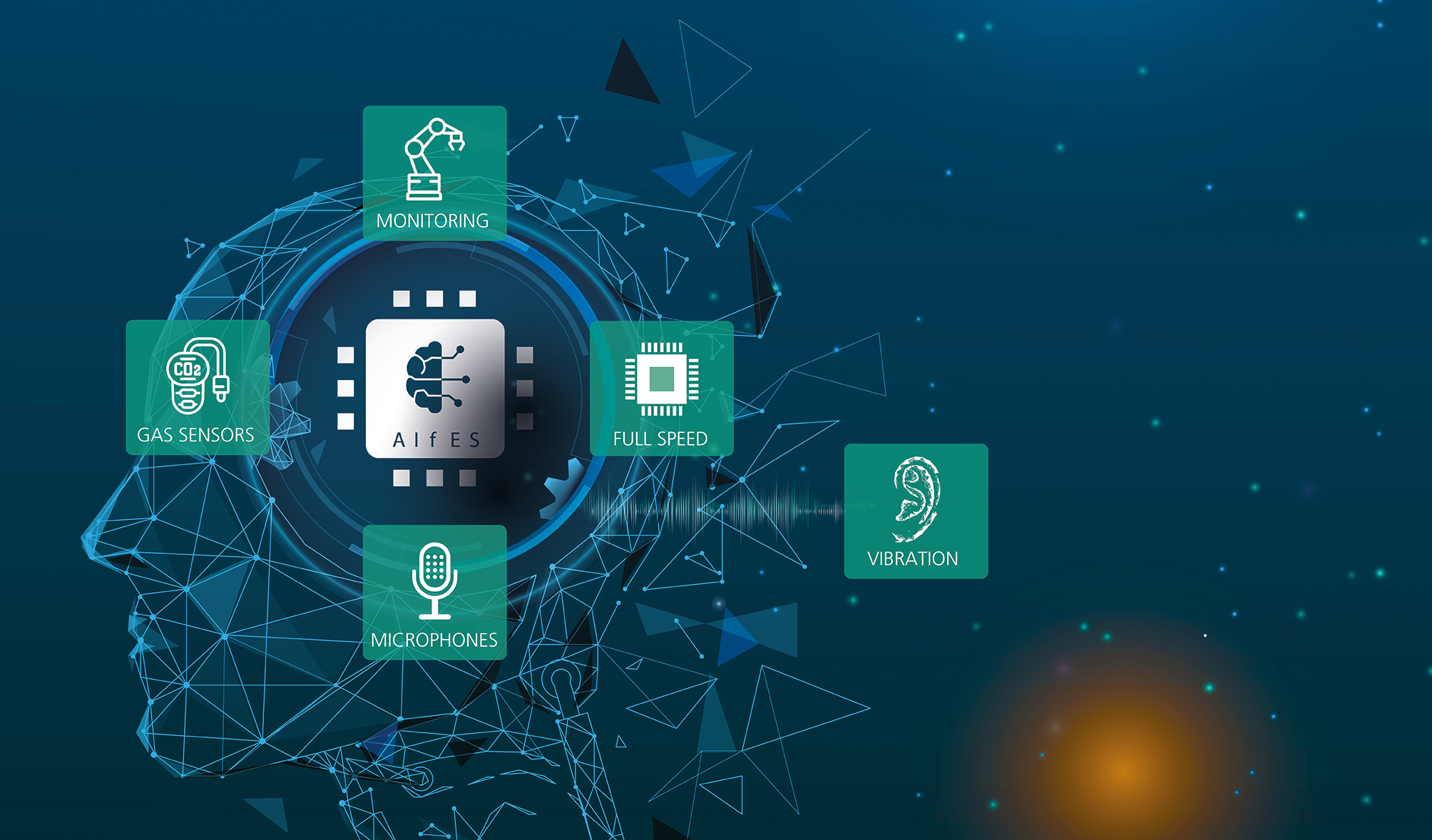