Forschung und Entwicklung | Kurznachrichten | Lesezeit: 2 Min.
Durch smarte Schallsensorik die Qualität von Lebensmitteln erhöhen und Rückrufkosten reduzieren: Erfolgreicher Abschluss vom BMWK-Projekt ISEP
Vorbeugung von Lebensmittelkontaminationen durch KI-basierte Überwachungsmethoden
Defekte Anlagen und Verunreinigungen von Lebensmitteln sind die zweithäufigste Ursache für Lebensmittelwarnungen in Deutschland. Im Projekt ISEP[1] hat das Fraunhofer IMS eine Lösung entwickelt, mit der solche Mängel für jeden einzeln abgefüllten Beutel schnell und zuverlässig erkannt werden. Dadurch wird eine höhere Qualität der Waren gewährleistet. Damit verbunden, können in Zukunft Lebensmittelverschwendung sowie hohe Schadensersatzansprüche und Rückrufkosten vermieden werden.
Mehr Sicherheit und Qualität unserer Lebensmittel und geringere Schadenskosten
Im Projekt ISEP wurde an der Entwicklung eines flexibel einsetzbaren Schallsensors zur autonomen Überwachung von Prozessen in der Lebensmittelproduktion geforscht. Durch das Vorhaben sollte eine zuverlässigere Messmethode eines schwierig zu erfassenden Maschinenzustandes als bei Vorgängermodellen entwickelt werden, um Verunreinigungen in Lebensmitteln zu vermeiden.
Referenzprozesse für das Projekt umfassen Abfüllanlagen, Fördereinrichtungen und Dosiersysteme aus der Lebensmittelindustrie. Exemplarisch wurde hierbei eine Schlauchbeutelmaschine zur Abfüllung von Lebensmitteln wie zum Beispiel Milchpulver, Kaffeebohnen oder Couscous betrachtet. Durch gezielte Optimierungen wurde die Zustandserkennung der Dosierschnecke kontinuierlich verbessert. Selbst unter erschwerten Bedingungen wie bei den im Abfüllprozess vergleichsweise großen und lauten Kaffeebohnen ist eine zuverlässige Überwachung des Zustands möglich.
Die Schallanalyse läuft dabei in folgenden Schritten ab: Zuerst werden die gesammelten Daten mithilfe von Merkmalsextraktion auf die für die Auswertung relevanten Informationen reduziert. Im Anschluss bewertet ein künstliches neuronales Netz die verbliebenen Informationen. Beide Schritte sind in eine an dem Schallsensor angeschlossene Auswerteeinheit mit Mikrocontroller integriert. Die Konfiguration des Sensors erfolgt automatisch auf Grundlage der bereits gesammelten Trainingsdaten.
Perspektive: Kostensensibles Training durch automatisierte Fehlererkennung
Das Projekt ISEP wurde zum 31. Mai 2023 erfolgreich beendet. Perspektivisch soll im nächsten Schritt an einer automatisierten Fehlererkennung der unterschiedlichen Abfüllprozesse geforscht werden. Bisher werden umfangreiche Trainingsdaten von funktionierenden und defekten Anlagen benötigt, um die Sensitivität des Sensors zu gewährleisten. Dies erfordert das gezielte Erzeugen verschiedener Defekte, was zusätzliche Kosten verursacht, und die Wiederverwendung der Maschinen gefährdet. Im Gegensatz dazu würde die automatisierte Fehlererkennung ein effizientes Training der Sensoren ausschließlich mit funktionsfähigen Daten ermöglichen.
[1] ISEP als Akronym für: Intelligenter Schallsensor zur Echtzeitüberwachung von Produktionsprozessen. Dieses Projekt wird vom Bundesministerium für Wirtschaft und Klimaschutz (BMWK) aufgrund eines Beschlusses des Deutschen Bundestages - unter dem Förderkennzeichen 16KN085620 – gefördert. Das Projekt erfolgte in Kooperation mit der ds automation GmbH.
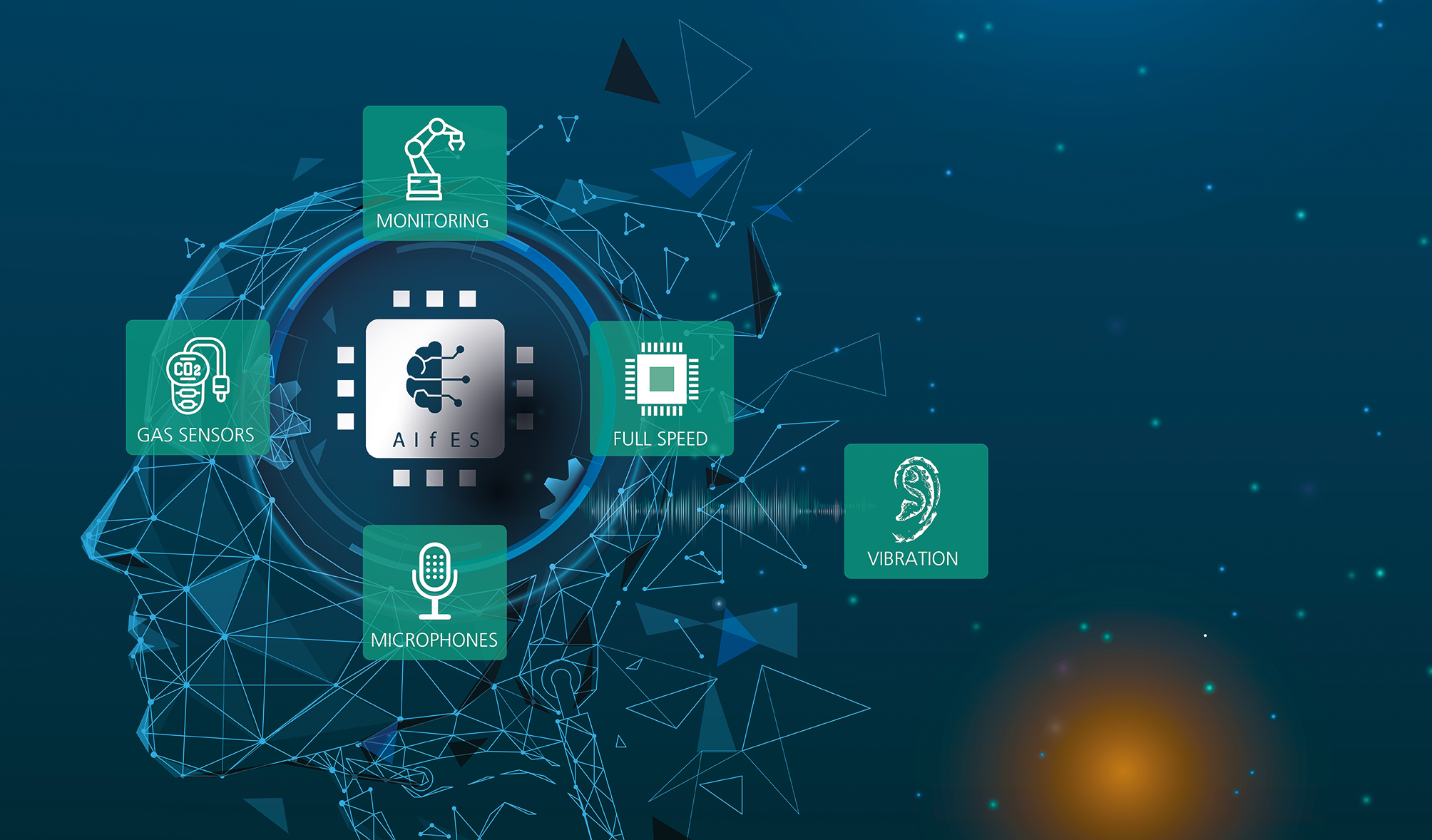