Research and development | Press release | Reading time 3 Min.
Annual savings in megatons of greenhouse gas emissions in industry and mobility through intelligent power electronics with novel gallium nitride semiconductors in motor controllers
Independence from fossil fuels and the switch to regenerative energy sources require extensive electrification of production and mobility. This increases the need for compact, energy-efficient, and reliable power electronics. In the PowerCare project[1], novel vertical gallium nitride power semiconductors as well as real-time failure models are developed and used in a motor drive. Here, PowerCare takes a new approach to the monitoring concept by using a miniaturized motor controller with integrated AI failure prediction. The project thus lays the foundation for the next evolutionary stage of intelligent, sustainable power modules.
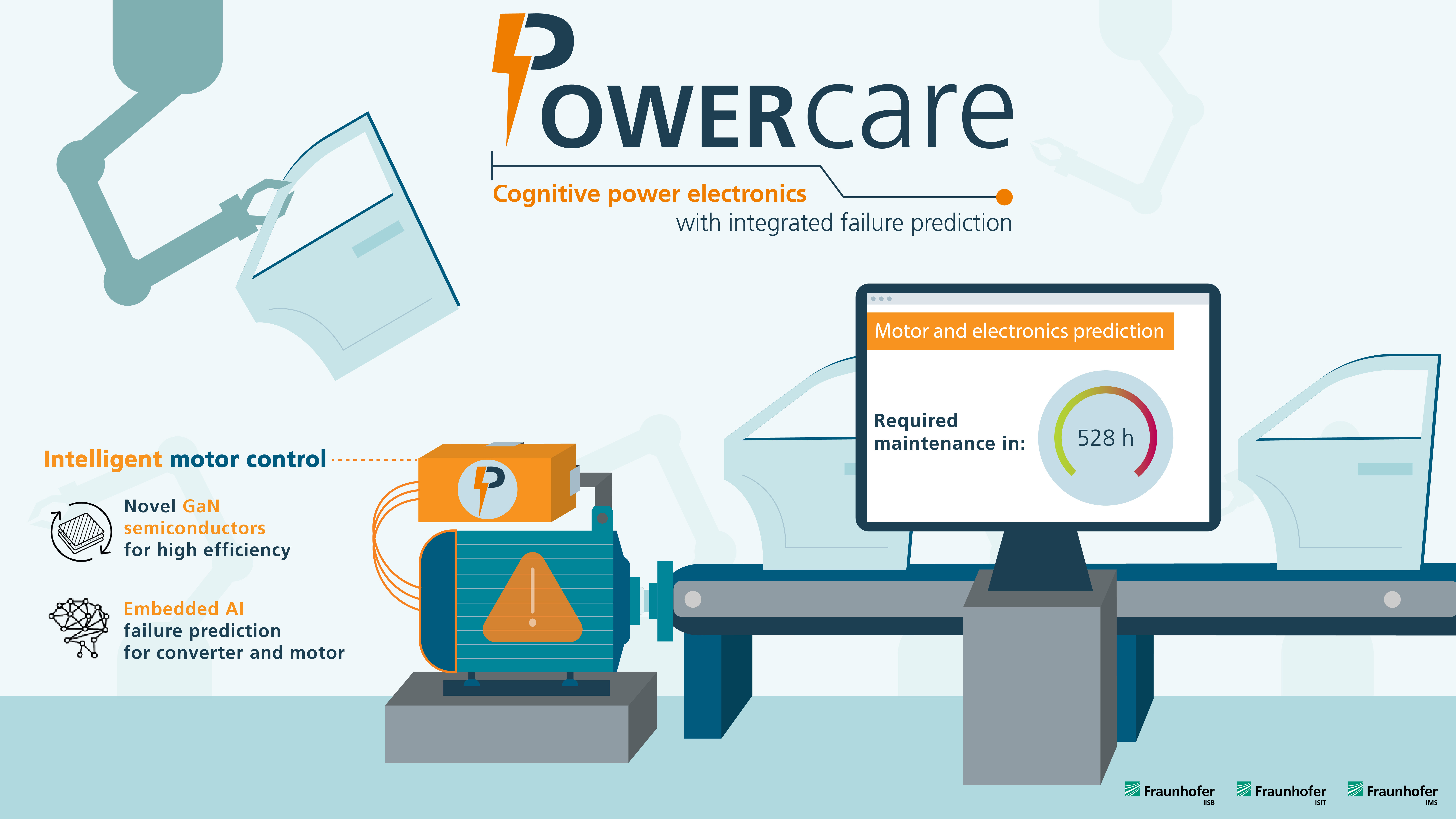
The innovative semiconductor material gallium nitride (GaN) offers enormous potential for the production of more compact as well as more efficient power modules due to its higher power density compared to other semiconductor materials. In fact, when converting the current from the socket to the drive, GaN semiconductors achieve a higher switching speed and thus lower power losses. If used on a widespread basis, savings of gigatons of greenhouse gases per year are possible compared with conventional semiconductors, which is roughly equivalent to emissions from 600 coal-fired power plants.[2] Industrial motors account for 30% of global electricity consumption and thus have a significant share in greenhouse gas emissions.[3] By using vertical GaN power semiconductors in industrial motor controls, PowerCare could achieve savings of around 124 megatons of CO₂e per year.[4]
However, the extensive use of new power electronics is also associated with risks in terms of their reliability. Particularly in the case of electric drive systems, on which human lives may depend, possible failures must be detected at an early stage. So far, GaN power modules with integrated failure prediction that are required for this are not available on the market. PowerCare not only aims to provide a solution for this, but could also be extended for the following use cases:
- Efficient and safe electric mobility
- Drones and electric aircraft
- Point-of-Load converters for data centers
- Safe cobots and medical robots
- Efficient and predictive PV inverters
An efficient GaN power module with local data evaluation, integrated condition monitoring, and failure prediction
In the project, the collaboration partners aim to develop AI-assisted failure prediction models running on a compact, high-performance microcontroller. The AI-enabled microcontroller will be assembled with high-efficiency GaN semiconductors to form a power module. A co-design of power semiconductors, microcontrollers, and prediction models will result in a miniaturized and energy-efficient module that can be directly integrated into the drives to be monitored. The aim is to detect power electronics faults at an early stage. Unexpected failures of these components would thus be minimized. For industrial applications, this offers the possibility of efficient and cost-saving maintenance planning. In the area of mobility applications and critical systems, increased safety can also be ensured in this way.
Application-oriented development of innovative power electronics with the help of strong partners from industry and research
The production of this type of intelligent power module will be enabled by the close cooperation of three Fraunhofer institutes. The development of the required components is divided up on the basis of their respective areas of expertise:
- Fraunhofer Institute for Integrated Systems and Device Technology IISB for AI-based condition monitoring of electric drives
- Fraunhofer Institute for Silicon Technology ISIT for vertical GaN devices including their failure models
- Fraunhofer Institute for Microelectronic Circuits and Systems IMS for RISC-V processors and embedded AI for failure predictions
Bringing together the competencies of the Fraunhofer institutes in PowerCare enables the rapid implementation of qualitative demonstrators. For a market-oriented development of cognitive power electronics, the project partners Siemens AG, X-FAB Dresden GmbH & Co. KG, NXP® Semiconductors Germany GmbH, and TU Dortmund University provide support and valuable practical feedback. If your company is also interested in the development status, the use of the results, or an application study, you are welcome to contact the project team via the contact box on this page.
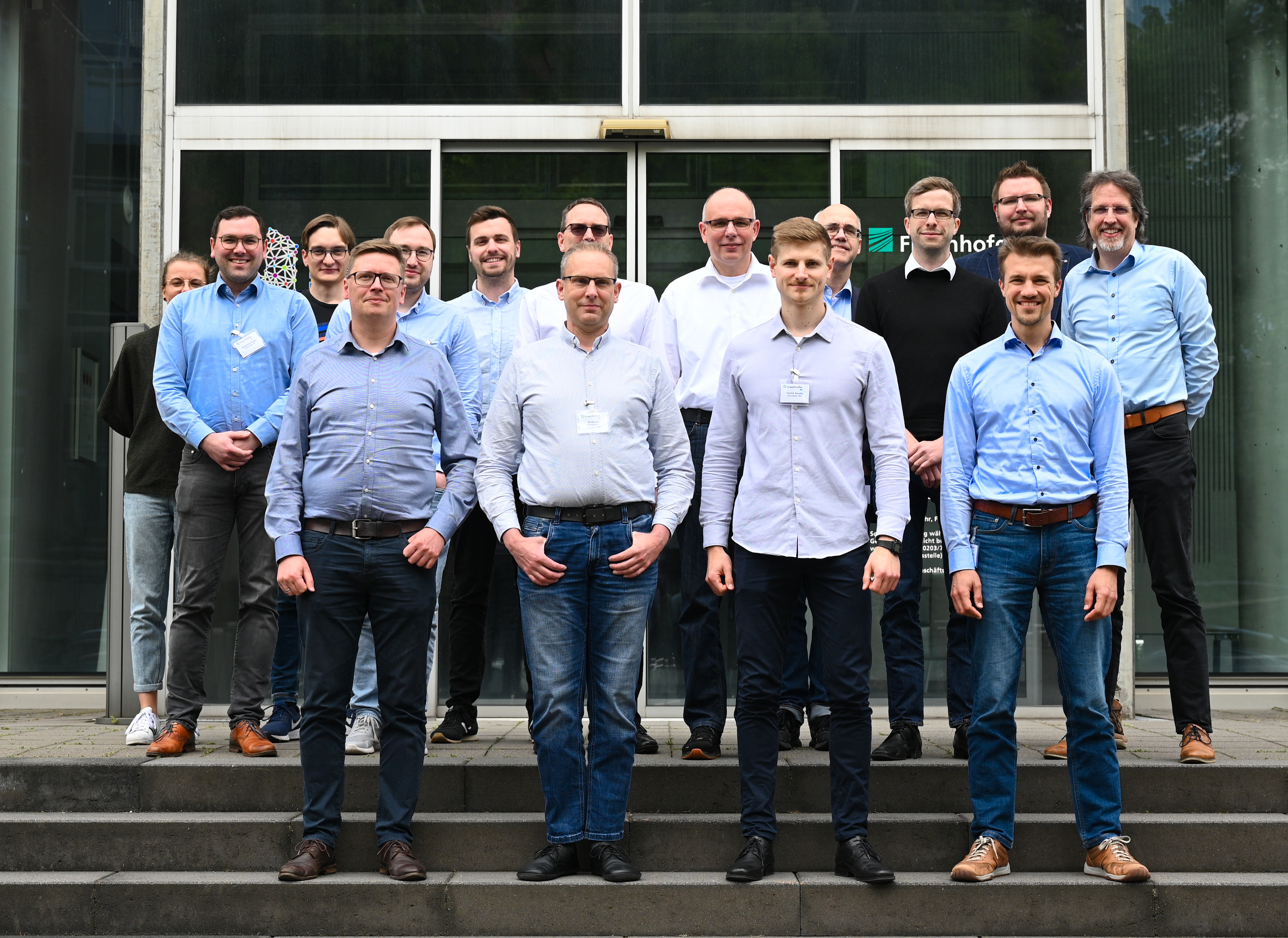
Fraunhofer IMS
Smart Sensor Systems for a safe, secure, and sustainable future: In numerous state-of-the-art research laboratories, Fraunhofer IMS works with more than 250 talented scientific employees and students on innovative microelectronic solutions. As a trusted research and development partner for industry, the institutes’ goal is to develop customized sensor systems for your specific needs in the areas of biomedical sensors, optical systems, open source semiconductors, embedded AI, technology services, and even quantum technology. The teams in the four business units – Health, Industry, Mobility, and Space and Security – are committed to implementing outstanding and versatile microelectronics that can be utilized across all your projects. For example, these solutions feature high integration capability, enormous energy efficiency and reliable functionality even under harsh conditions.
Research Fab Microelectronics Germany (FMD)
The Fraunhofer IMS is part of the Forschungsfabrik Mikroelektronik Deutschland (FMD) - a cooperation of the Fraunhofer Group for Microelectronics with the Leibniz Institutes FBH and IHP. As a pioneer for cross-site and cross-technology collaboration, the FMD addresses current and future challenges in electronics research and provides important impulses for the development of elementary innovations for the world of tomorrow.
https://www.forschungsfabrik-mikroelektronik.de/en.html | Also visit our virtual 3D showroom at https://fmd-insight.de/showroom
[1] This work was supported by the Fraunhofer Internal Programs under Grant No. PREPARE 40-06175.
[2] Source: Navitas (2022): »Sustainability Report 2021«
[3] Source: Infineon (2020): »Industrial Drives: Overview and Main Trends«
[4] Assumption: efficiency increase of 3% when using quasi-vertical GaN MOSFETs instead of Si FETs.